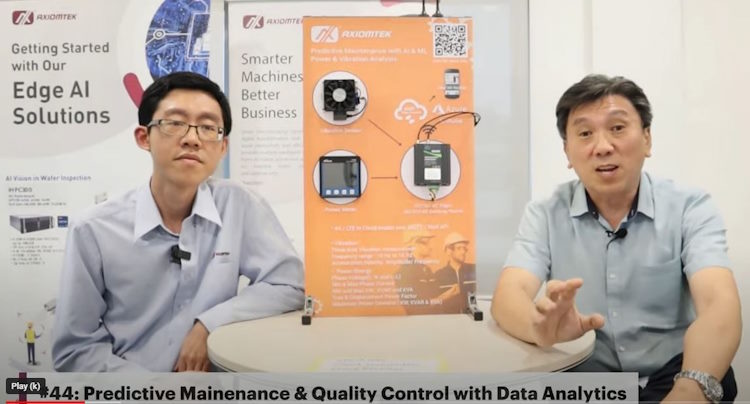
The manufacturer’s potential losses due to unplanned downtime and possible solutions to mitigate them were the central topics discussed during the live sharing session on April 12, 2024, in the “Sembang AIoT” live talk hosted by AIoTmission and Axiomtek Malaysia.
Below are some of the potential losses:
Production Losses: The most immediate impact is the loss of production output during the downtime period. This directly affects the ability to fulfill orders and meet customer demand, potentially leading to missed sales opportunities and dissatisfied customers.
Revenue Losses: With decreased production comes reduced revenue. The longer the downtime persists, the greater the financial impact on the manufacturer’s bottom line.
Wasted Materials: During downtime, raw materials may sit unused or partially processed, leading to wasted resources and increased material costs.
Labor Costs: Even though production may halt during downtime, labor costs often continue as employees may still need to be paid despite not actively working on production tasks.
Overtime and Recovery Costs: Once production resumes, manufacturers may need to implement overtime hours or expedited processes to catch up on missed production targets, resulting in additional labor costs.
Equipment Repair or Replacement: Depending on the cause of the downtime, there may be repair or replacement costs for damaged machinery or equipment, further adding to the financial burden.
Reputation Damage: Extended or frequent downtime can damage the manufacturer’s reputation among customers and suppliers, leading to potential long-term impacts on relationships and future business opportunities.
Overall, the losses incurred during unplanned downtime can be significant, not only in terms of immediate financial impact but also in terms of long-term consequences for the manufacturer’s competitiveness and reputation in the market.
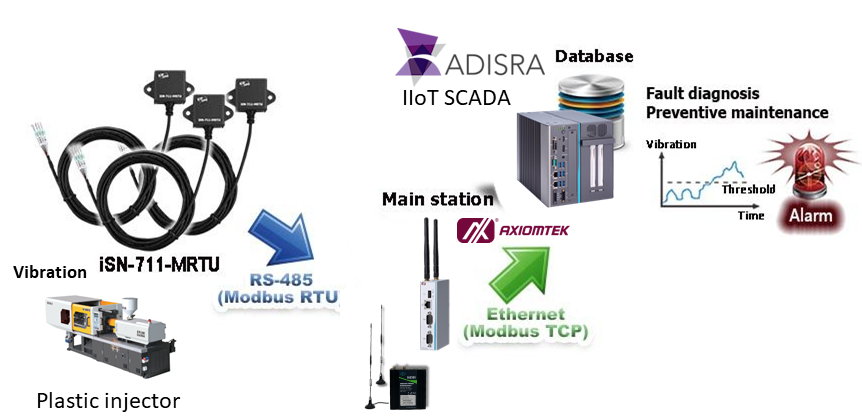
Introducing the AI Data analytics to the to the Plastic injection machine as a solution to reduce or avoid unplanned downtime.
An AI predictive analytics solution for a plastic injection machine could involve the following components:
Data Collection: Gather data from various sources within the manufacturing process, including IIoT sensor data from the injection machine itself (e.g., Vibration,temperature, pressure, cycle time), historical performance data, maintenance records, environmental conditions, and quality control data.
Data Preprocessing: Clean and preprocess the collected data to remove noise, handle missing values, and normalize the data for analysis. This step may also involve feature engineering to extract relevant features from the raw data.
Predictive Modeling: Develop machine learning models to predict potential issues or failures in the plastic injection machine. This could include regression models to predict machine performance metrics (e.g., cycle time, defect rate), classification models to detect anomalies or impending failures, and time series forecasting models to predict future machine behavior.
Feature Selection and Engineering: Identify the most relevant features that contribute to the predictive accuracy of the models. This may involve techniques such as correlation analysis, feature importance ranking, and domain expertise to select the most informative features for prediction.
Model Training and Evaluation: Train the predictive models using historical data and evaluate their performance using appropriate metrics (e.g., accuracy, precision, recall, F1-score). Iteratively refine the models to improve their accuracy and generalization to new data.
Real-time Monitoring and Alerting: Deploy the trained models to a real-time monitoring system that continuously analyzes incoming data from the plastic injection machine. The system can generate alerts or notifications when it detects abnormal patterns or potential issues that require attention from operators or maintenance personnel.
Integration with Maintenance Systems: Integrate the predictive analytics solution with the manufacturer’s existing maintenance management systems to schedule preventive maintenance activities proactively based on the predictions generated by the models. This can help minimize unplanned downtime and reduce the risk of equipment failures.
Continuous Improvement: Continuously monitor the performance of the predictive models in production and collect feedback to refine the models further. This may involve retraining the models periodically with new data to adapt to changing operating conditions and improve predictive accuracy over time. When predictive analytics is applied together with the OEE tracking system, it will ensure the process is running with full efficiency and maximum capacity.
By implementing an AI predictive analytics solution for the plastic injection machine, manufacturers can enhance operational efficiency, reduce downtime, optimize maintenance schedules, and ultimately improve the overall productivity and profitability of their manufacturing processes.
To watch the detail live detail. you may visit our youtube channel at