AIoT OEE Insight Connect Cloud Dashboard
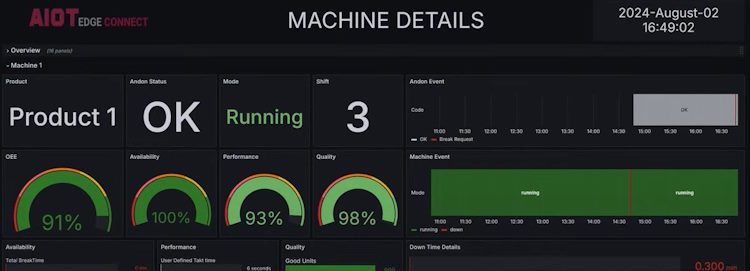
AIoT OEE Insight Connect Cloud Dashboard is part of the OEE Insight Tracking for the production floor with the aim of a screen overview of the OEE ( Overall Equipment Effectiveness) Dashboard that tell the whole story about your your process.
- Stack light tracker
- IIoT Edge Gateway
- Local SCADA Dashboard
- Andon Tablet / Down Time Reason Tablet
- AIoT Edge Connect Cloud Dashboard / On-prem Cloud Hub
With all the components listed above it forms a complete and comprehensive OEE Insight Tracker it will provide not only the OEE KPI index but a detailed insight into your process where it includes:-
- Reasons for Time with interval
- Type of Rejects within the product
- 6 Key lossess in the process
What are the 6 key lossess in the manufacturing process:-
The six losses in Overall Equipment Effectiveness (OEE) are the primary sources of waste and inefficiency in manufacturing processes. They are typically categorized into three main groups: Availability Losses, Performance Losses, and Quality Losses.
Availability Losses:
Unplanned Downtime: This includes unexpected equipment failures and breakdowns.
Planned Downtime: This includes scheduled maintenance, changeovers, setup, and adjustments.
Performance Losses:
Reduced Speed: This occurs when equipment is running but not at its maximum possible speed. Causes can include worn-out machinery, suboptimal settings, or operator inefficiencies.
Minor Stops: These are brief, unplanned stops in production due to minor issues like jams, blockages, or adjustments.
Quality Losses:
Process Defects: These occur during stable production and result in products that do not meet quality standards. Causes can include improper machine settings, worn tools, or suboptimal raw materials.
Reduced Yield: This refers to losses due to product defects during the startup phase of production, such as scrap or rework needed after initial runs.
Addressing these six losses is critical for improving OEE and enhancing overall manufacturing efficiency.
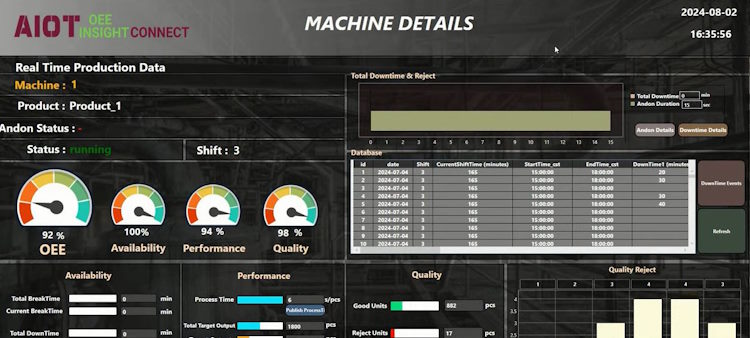
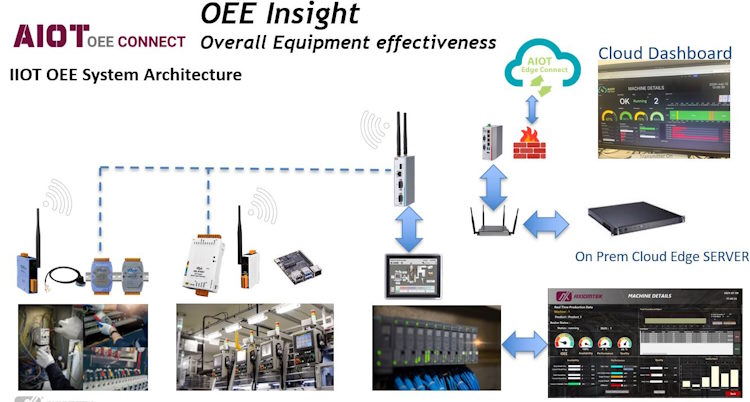
In the AIoT OEE insight, Connect also supports Andon System Tracking.
An Andon system is a visual and audible alert system used in manufacturing to signal the occurrence of a problem or abnormal condition in the production process. It is a key component of lean manufacturing and the Toyota Production System, aimed at improving communication and facilitating quick response to issues on the production floor. Here are the main elements and functions of an Andon system:
Visual Signals: Typically, Andon systems use lights (often in different colors) to indicate the status of the production process. Common colors and their meanings include:
Green: Normal operation.
Yellow: Attention required or minor issue.
Red: Significant problem or stop in production.
Audible Alerts: These can include alarms, buzzers, or other sounds to attract attention to the issue.
Pull Cords or Buttons: Operators can manually activate the Andon system by pulling a cord or pressing a button when they identify a problem.
Display Boards: These boards can show detailed information about the nature of the problem, the location, and any necessary actions to resolve it.
Functions of an Andon System:
Immediate Notification: It provides immediate awareness of issues, enabling quick response and resolution, minimizing downtime and preventing defects from propagating through the production line.
Empowerment of Workers: Operators are empowered to stop the production line if they detect a problem, ensuring that quality and safety are prioritized over meeting production targets.
Communication: It facilitates clear communication across the production floor, ensuring that all relevant personnel are aware of issues in real-time.
Continuous Improvement: By logging and analyzing Andon alerts, manufacturers can identify recurring issues, implement corrective actions, and continuously improve processes.
In essence, an Andon system is a tool for enhancing transparency, accountability, and responsiveness in the manufacturing process, ultimately leading to higher efficiency, better quality, and reduced waste.
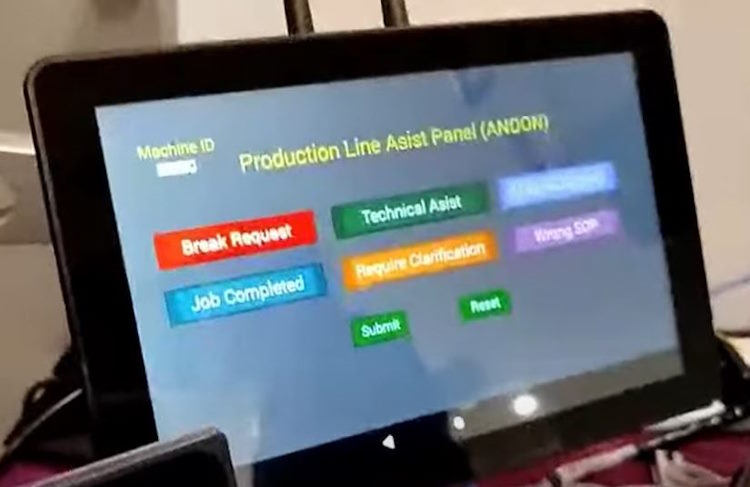
The Wireless Andon Tablet or andon Wireless terminal is used to provide a calling system in the Andon Tracker to talk to the host so that the escalation of the alert like technical assistance, break request, job complete etc to create a effective communication among the team members.
The AIoT OEE Insight Connect includes the tracking of the time response on the Andon system.
Tracking the time response to an Andon system is crucial for several reasons related to efficiency, quality, and continuous improvement in manufacturing:
Minimizing Downtime:
Quick Resolution: Prompt response to Andon alerts reduces the time equipment is non-operational, thereby minimizing downtime and maintaining productivity.
Identifying Bottlenecks: Analyzing response times helps identify delays in addressing issues, enabling targeted interventions to streamline the process.
Improving Process Efficiency:
Resource Allocation: Understanding how long it takes to respond to different types of issues can help allocate resources more effectively, ensuring the right personnel and tools are available when needed.
Optimizing Workflows: Insights from response time tracking can lead to optimized workflows and better coordination among team members.
Enhancing Quality Control:
Preventing Defects: Faster response times mean problems are addressed before they can escalate, preventing defects from continuing down the production line.
Consistency: Monitoring and improving response times ensures consistent handling of issues, contributing to more uniform product quality.
Empowering Continuous Improvement:
Data-Driven Decisions: Detailed data on response times allows for data-driven decision-making, identifying patterns and recurring issues that can be addressed systematically.
Benchmarking and Goals: Tracking response times provides benchmarks for performance, helping set realistic goals for improvement and measure progress over time.
Employee Performance and Training:
Performance Metrics: Response times can be used as a performance metric for operators and maintenance teams, highlighting areas for improvement or additional training.
Training Needs: Consistently long response times may indicate a need for additional training or changes in procedures to better equip staff to handle issues promptly.
Customer Satisfaction:
Reliability: Efficient resolution of issues leads to more reliable production schedules and delivery times, improving overall customer satisfaction.
Quality Assurance: Ensuring quick responses to quality issues maintains high product standards, which is critical for customer trust and brand reputation.
In summary, tracking the time response to an Andon system is essential for maintaining high operational efficiency, ensuring quality control, facilitating continuous improvement, and ultimately delivering better value to customers.
To find out about the AIOT OEE Insight Connect you may watch the video on Youtube with some related Demo at this link: –