The Planned Stop - Six OEE Big Losses
We can understand unplanned downtime, but why planned stop? 🤔
In manufacturing, planned stops represent a major category of production losses and it is part of the OEE six big losses. These are intentional halts in machine operation—such as for model changes, tool changes, or scheduled maintenance—that can heavily impact OEE (Overall Equipment Effectiveness) if not managed properly.
A key tool in managing and visualizing these stops is the Andon system—a real-time visual indicator (typically using stack lights with 3 or 4 colors) that communicates machine or process status directly from the production floor. A red or blue light, for instance, may signal a planned stop, alerting operators and maintenance teams in real time.
While planned downtime is necessary, poor planning or execution can erode process availability and drag down your OEE score. That’s why tracking and optimizing these stops is vital.
Common Causes of Planned Stops:
* Model or Tool Changes – Switching between product variants requires precise setup and reconfiguration.
* Scheduled Maintenance – Preventive checks that ensure long-term machine health but interrupt short-term productivity.
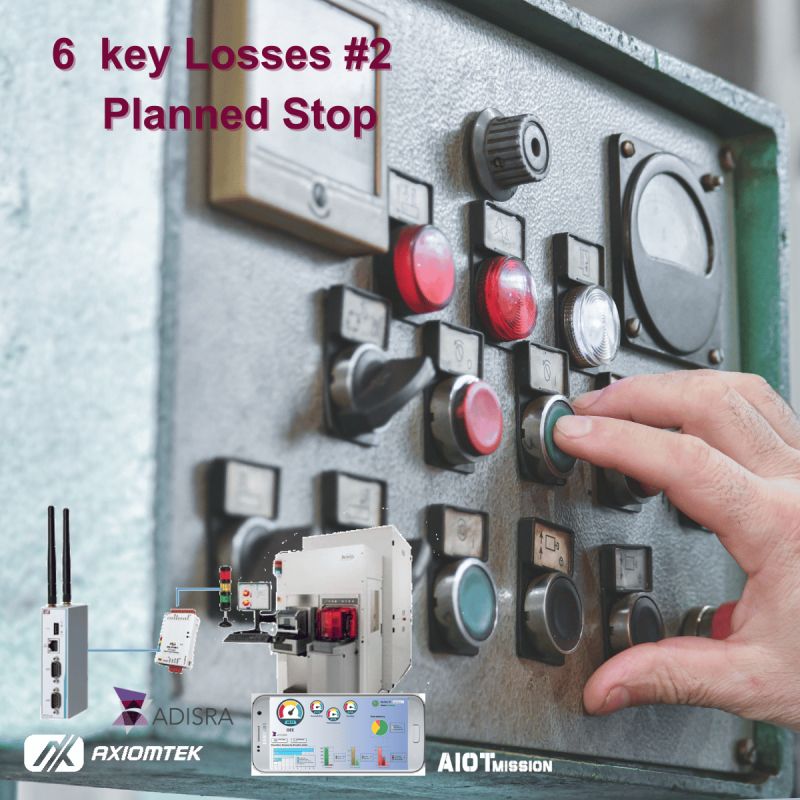
Key Diagnostic Points to Track:
- Duration of tooling/model changes
Transition details between previous and next models - Responsible personnel
- Root cause of each planned stop
With the right IIoT (Industrial Internet of Things) setup, this tracking becomes seamless. For example, using a smart HMI system like AdisRA SmartView paired with Axiomtek graphical terminals or gateways allows operators to log data directly at the source. These systems can integrate with existing machine I/O for automated data collection.Once collected, the data becomes a goldmine for AI-driven analytics. With historical insights, your system can suggest the most efficient model sequences, highlight inefficiencies by operator or process, and fuel your Kaizen efforts for continuous improvement.This is where AIoT (Artificial Intelligence + IoT) transforms from buzzword to business impact—turning data into smarter decisions and enhanced productivity.
#oeeinsightconnect #6biglosses #PlannedDowntime #SmartManufacturing #IIoT #AIoT #LeanManufacturing #Kaizen #DigitalTransformation #AndonSystem #2ndmalaysiatakeoff
Planned stops are classified under “unavailability” in OEE calculations and are typically unavoidable, such as maintenance, product changeovers, or compliance-related inspections. Since these events are necessary, the key to minimizing their impact lies in reducing both their frequency and duration as much as possible.
One of the most effective strategies to limit the impact on OEE is implementing dynamic scheduling, especially when managing multiple SKUs with different production requirements. This approach involves planning the optimal time slots for each SKU based on production needs, machine availability, and changeover times.
To do this effectively, real-time shop floor data is essential. It provides insights into machine performance, actual downtime durations, and the best timing for planned stops. That allow production teams to schedule stops in a way that aligns with lower-demand periods or natural production idle time.Â