Six Big Losses in OEE #3 The Slow Cycle
SLOW –> BIG !😉
Why? When it is concerning the heartbeat of the production, so it is BIG!🧨
The 6 Big losses #3 -The Slow Cycle.
In any manufacturing environment, cycle time is more than just a metric—it’s the heartbeat of the production system. Each completed cycle represents a unit of output, and when those beats slow down, so does productivity.
That’s why monitoring cycle time is so critical. It tells you, in real time, whether your production line is healthy and performing at its best—or if there are hidden inefficiencies slowing things down.
When you walk through a modern production floor, you’ll often see digital boards displaying Target Output vs. Actual Output. This real-time feedback loop creates operator awareness, helping them stay aligned with expected production goals. It also acts as a subtle productivity cue, letting teams know if the “heartbeat” of the process is slowing.
This slowdown—known as a slow cycle—can be caused by several factors:
* Machine degradation, where equipment no longer operates at optimal
speed
* Manual processes, where human pace varies
* Process inefficiencies, often invisible without proper tracking
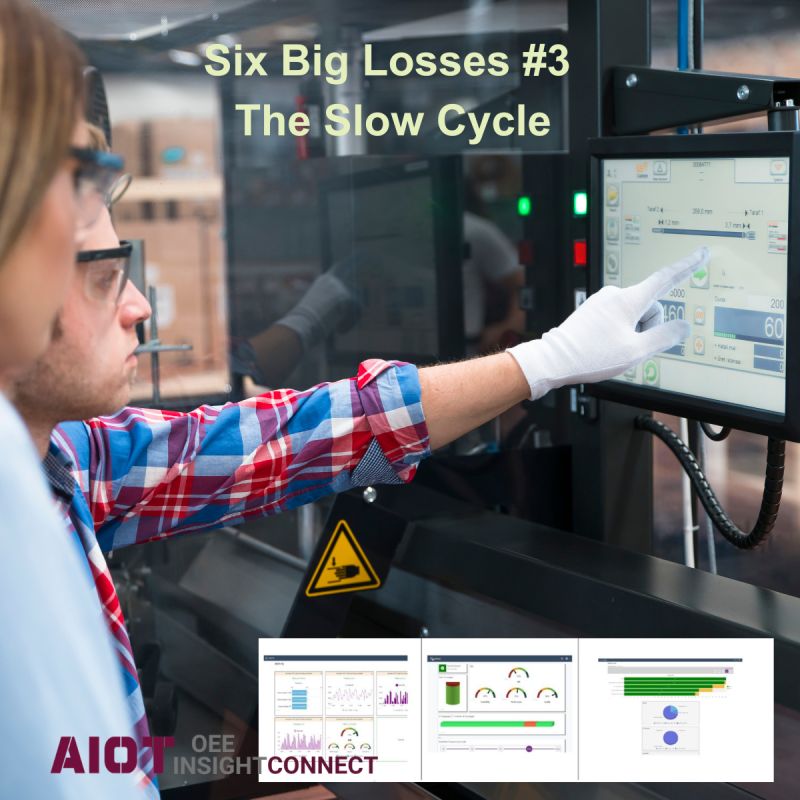
Slow Cycle Impact to OEE
For human-related slowdowns, visible target indicators help improve pace and consistency. But when machines slow down, we need a more technical approach to diagnose and resolve the issue.
To effectively track and optimize cycle time, it’s important to understand the three core definitions:
* Ideal Cycle Time – The fastest time a process can complete a cycle under
optimal conditions
* Average Cycle Time – The mean time per cycle over a defined period
* Actual Cycle Time – The time taken for each individual cycle
These measurements directly impact the Performance component of OEE (Overall Equipment Effectiveness), making cycle time a central focus in any productivity improvement effort. Cycle time can be captured through several techniques:
* Machine I/O Signals – Using input/output signals to timestamp each cycle
* Stack Light State Changes – Tracking transitions in stack light colors to
detect cycle completion
* Computer Vision AI – A cutting-edge solution that uses cameras and AI to:
– Detect human gestures or task completions
– Monitor the entire flow of a process visually
– Recognize stack light color changes to infer machine status
These modern methods allow for automated, real-time cycle tracking, even in environments where traditional sensors are not viable.
Slow cycles, if left unchecked, silently drain your productivity. By benchmarking against ideal or average cycle times, you can identify when performance dips and take corrective actions—before small inefficiencies snowball into larger losses.
With the right technology, be it sensor-based, vision AI, or hybrid solutions, you gain the insight needed to optimize your cycle time, improve performance, and ultimately, boost your OEE index.
#OEEinsight #slowcycle #6biglosses #aiot #aiotoeeinsightconnect #smartmanufacturing #unplanneddowntime