Vision AI on digital Display in Sembang AIoT live Channel
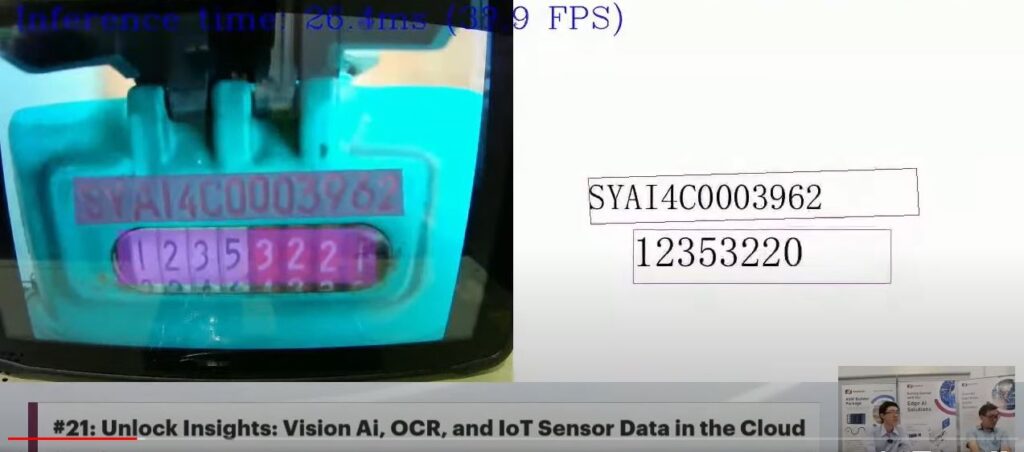
The extended presentation of “Sembang AIoT” commenced with a focus on Vision AI OCR. In this context, digital meters served as a primary data source for the AI OCR engine, facilitating the extraction of text from various meter types and indicators.
Furthermore, the discussion revolved around the concept of non-intrusive data extraction, prompting a recollection of our initial non-intrusive data extraction kits, which were showcased at an IoT summit event in Penang hosted by Intel Malaysia. During this demonstration, we exhibited non-intrusive data extraction using an industrial ebox IPC system to intercept VGA output from simulated machine data. Subsequently, video content was captured and extracted using an OCR engine running on the ebox IPC, as depicted in the accompanying image. Additional visual material can be found on our parent company Axiomtek Malaysia’s Facebook page by searching for “non-intrusive.”
The live demonstration proceeded to encompass a new array of meters and indicators, referred to as “Digital Data Extraction within Digital.” This phase involved scanning all digital indicators with a camera and utilizing the Intel Openvino AI engine, which was operational on the Axiomtek AI Edge computer, to perform AI OCR on diverse digital displays for data extraction.
For further insights and interactive explanations, please visit our live channel and explore additional examples.
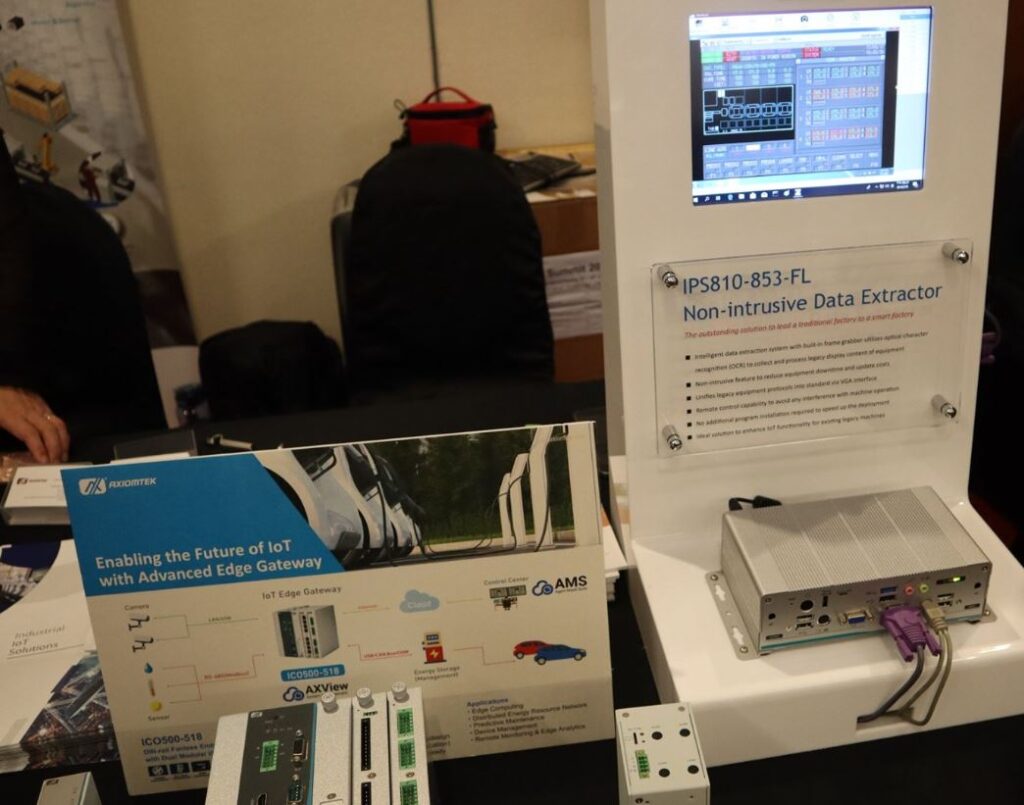
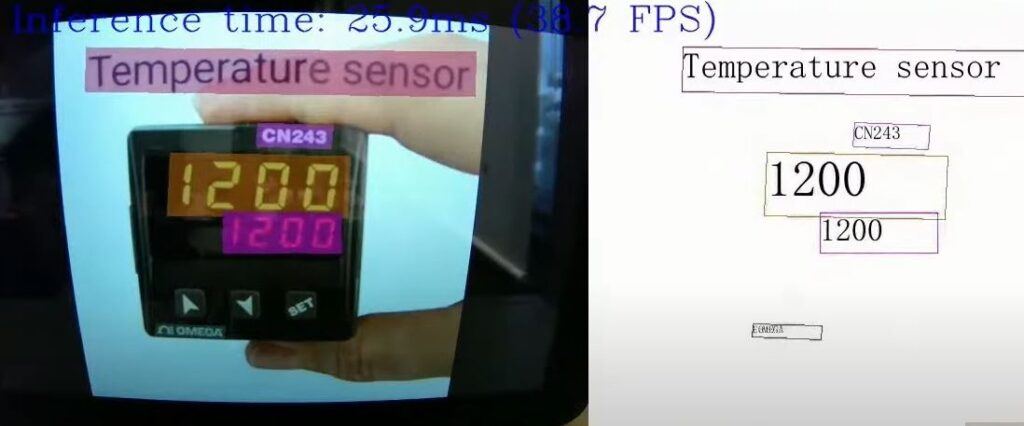
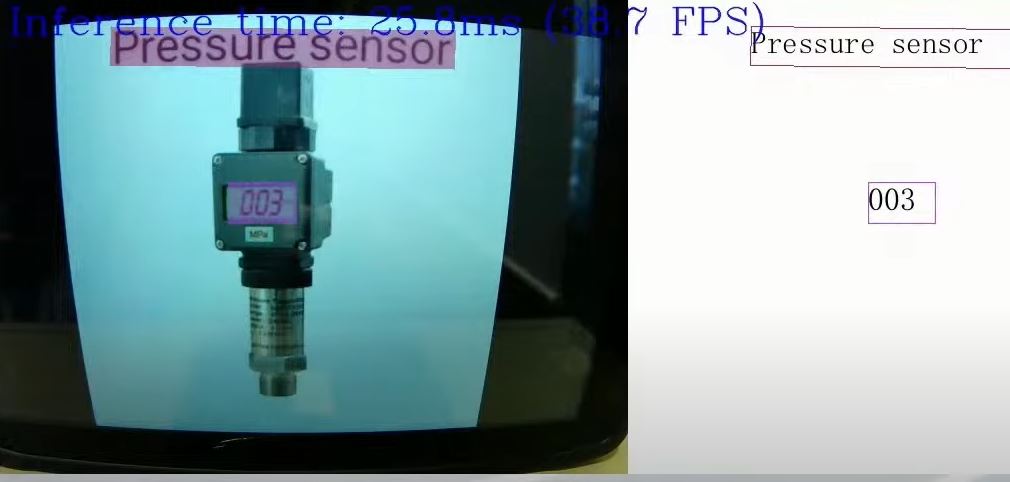
The demonstration of the Vision OCR AI on the Temperature controllers. On the right, the pressure transmission indicator is used to let the Axiomtek AI edge perform the AI OCR inferencing.
see more interactive explanations in the live channel.
RTD sensors IIoT applications -2 wires, 3 wires and 4 wires explained
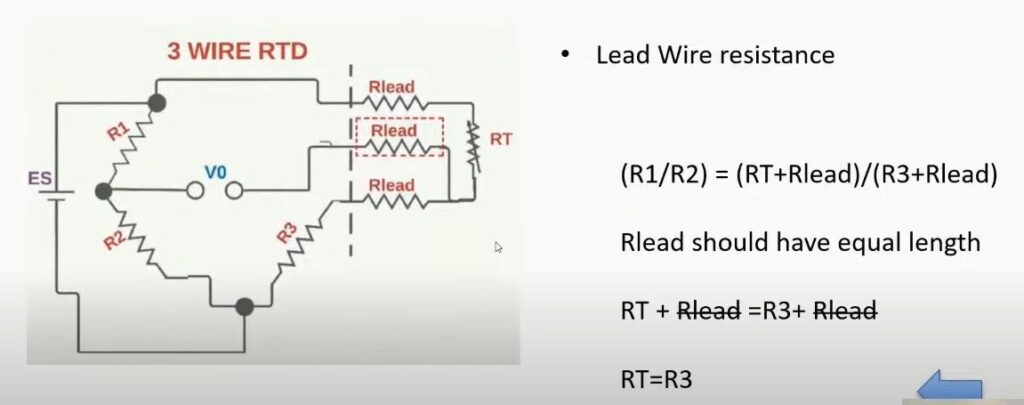
The demonstration included a dedicated discussion on industrial RTD (Resistance Temperature Detector) temperature sensors, highlighting their critical relevance in practical industry applications. Our aim was to provide in-depth insights into the usage of 2-wire, 3-wire, and 4-wire RTD sensors, elucidating the distinctions, advantages, disadvantages, and the considerations involved in selecting the most suitable RTD sensor for a specific application.
Temperature stands as a pivotal parameter in numerous industrial processes. Consequently, it assumes paramount importance for Industrial Internet of Things (IIoT) applications, necessitating an accurate understanding and appropriate utilization within the realm of measurement.
To gain a comprehensive understanding of these topics, we encourage you to explore our interactive live session, commencing from the 27th minute onwards. You can locate this session by conducting a search on YouTube using the query “YouTube #21 Sembang AIoT.” Should you encounter any difficulty in locating the content, please do not hesitate to inform us, and we will provide further assistance.
2-wire, 3-wire, and 4-wire RTD (Resistance Temperature Detector) sensors are commonly used for measuring temperature in various industrial and scientific applications. The main differences between them lie in their wiring configurations and their impact on measurement accuracy and compensation for lead wire resistance. Here are the key differences and their typical applications:
2-Wire RTD Sensors:
Wiring Configuration: A 2-wire RTD sensor has two wires: one for the RTD element and one for the lead wire.
Advantages:
Simplicity of wiring.
Cost-effective.
Disadvantages:
Less accurate compared to 3-wire and 4-wire configurations due to the inability to compensate for lead wire resistance.
Applications: Used in applications where high accuracy is not critical, and cost and simplicity are primary concerns. Common in basic temperature measurement tasks.
3-Wire RTD Sensors:
Wiring Configuration: A 3-wire RTD sensor has three wires: two for the RTD element and one for the lead wire. The two wires for the RTD element are connected in a series.
Advantages:
Provides compensation for lead wire resistance, improving accuracy.
Offers good accuracy while remaining cost-effective.
Disadvantages:
Not as accurate as 4-wire configurations but suitable for many applications.
Applications: Used in applications where moderate accuracy is required, and compensation for lead wire resistance is necessary. Common in industrial temperature monitoring and control.
4-Wire RTD Sensors:
Wiring Configuration: A 4-wire RTD sensor has four wires: two for the RTD element and two for the lead wire. The two sets of wires are connected in parallel.
Advantages:
Highest accuracy among the three configurations.
Accurate compensation for lead wire resistance.
Disadvantages:
More complex wiring and potentially higher cost.
Applications: Ideal for applications demanding high accuracy and precision, such as laboratory and scientific measurements, calibration standards, and critical industrial processes.
In summary, the choice between 2-wire, 3-wire, and 4-wire RTD sensors depends on the level of accuracy required, the budget constraints, and the specific application. While 2-wire RTDs are the simplest and most cost-effective, they are less accurate. 3-wire RTDs strike a balance between cost and accuracy, making them suitable for many industrial applications. 4-wire RTDs provide the highest accuracy but come at a higher cost and complexity, making them suitable for precision measurements and calibration standards.
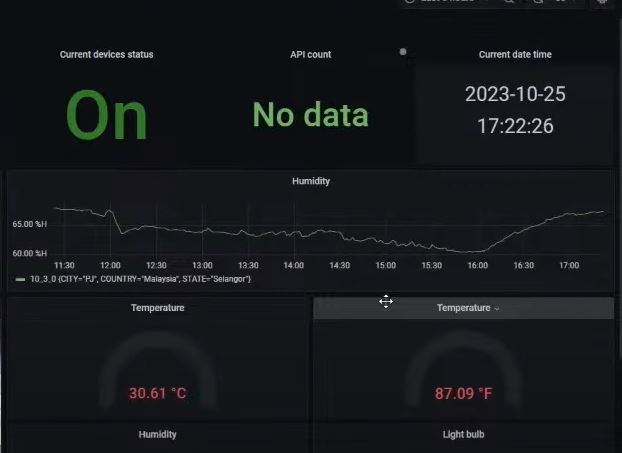
AIoT Edge Connect IIoT cloud platform featuring:-
- Data Visualization on the dashboard
- Historian Data logging
- Alert management ( Whatsapp, SMS , Telegram and Email )
watch us live at the link blow: