Boosting Manufacturing Efficiency with AIOT OEE Insight Connect
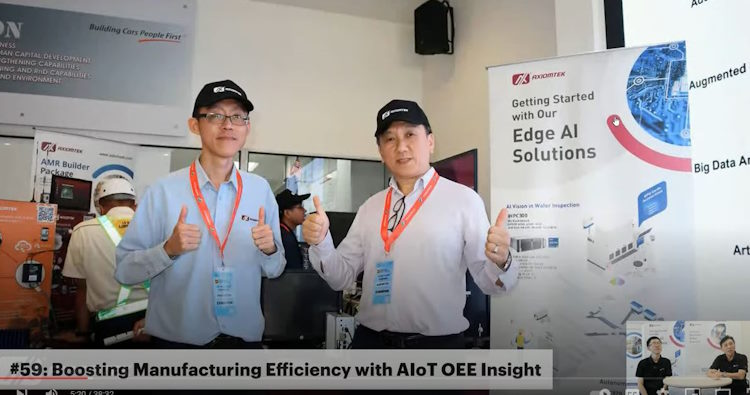
In this episode of live sharing on the 26th of July 2024, we delved deeper into boosting efficiency with OEE Tracking in manufacturing. This discussion builds on AIOTmission’s recent participation with Axiomtek Malaysia in a mini exhibition hosted by a local automotive manufacturer. At the event, we showcased three key technologies:
Industrial IoT
Industrial AI
Autonomous Mobile Robots (AMR)
Interestingly, during the three-day exhibition, all participants were required to wear hats at all times, which led to the introduction of the “Black Cap.”
Mini Exhibition at the Local Automotive Manufacturer
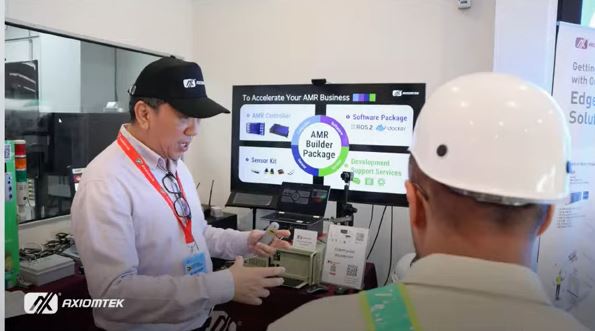
What is OEE? Where is it originated ?
Some background about OEE ( Overall Equipment Effectiveness):-
Overall Equipment Effectiveness (OEE) is a key performance indicator used to measure the efficiency and effectiveness of manufacturing processes. It provides a comprehensive view of how well a manufacturing operation is performing by tracking three critical aspects:
Availability: This measures the percentage of scheduled production time that the equipment is actually up and running.
Performance: This evaluates the speed at which the equipment operates compared to its maximum potential speed.
Quality: This assesses the proportion of good products produced versus the total number of products started.
The formula for calculating OEE is:
OEE = Availability × Performance × Quality
OEE= Availability × Performance × Quality
Each component is calculated as follows:
Availability = Operating Time / Scheduled Production Time ( /=dividded)
Performance = (Ideal Cycle Time x Total Count) / Operating Time ( x= Multiply)
Quality = Good Count / Total Count
OEE was developed by Seiichi Nakajima in the 1980s as part of the Total Productive Maintenance (TPM) philosophy, which originated in Japan. Nakajima introduced OEE as a method to help manufacturers identify and eliminate waste in their production processes, ultimately improving productivity and efficiency.
The main objective of Total Productive Maintenance (TPM) is to maximize the overall efficiency of production equipment and processes. TPM aims to achieve this by involving all employees in the maintenance process and integrating maintenance activities into everyday operations. The key goals and objectives of TPM include:
Zero Breakdowns:
Prevent equipment failures and unplanned downtime through proactive and preventive maintenance strategies.
Zero Defects:
Improve the quality of the products by ensuring that equipment operates correctly and consistently, minimizing defects and rework.
Zero Accidents:
Enhance workplace safety by maintaining equipment in optimal condition, reducing the risk of accidents and injuries.
Increased Equipment Effectiveness:
Optimize the performance of machinery by improving availability, performance, and quality, as measured by Overall Equipment Effectiveness (OEE).
Employee Involvement and Ownership: Foster a sense of ownership and responsibility among all employees, encouraging them to participate in maintenance activities and continuous improvement efforts.
Reduced Maintenance Costs: Lower the costs associated with maintenance by implementing efficient maintenance practices, reducing breakdowns, and extending the lifespan of equipment.
Continuous Improvement (Kaizen): Promote a culture of continuous improvement where employees are encouraged to identify and implement incremental changes that enhance productivity and efficiency.
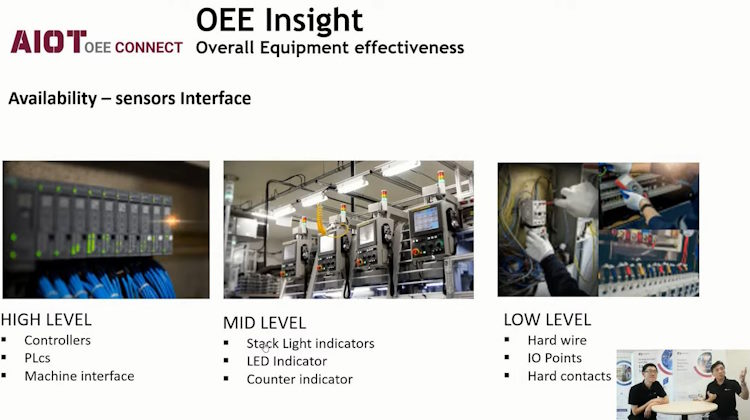
Connecting the Dots from the Shop Floor:
To complete the OEE calculation, we need the assistance of IIoT devices to connect and gather shop floor data. We categorize the interfaces into three main levels:
Low-Level Interface:
This is necessary when dealing with legacy machines or equipment that cannot be directly linked via a communication channel. Hard wiring, I/O points, and contacts must be established to gather machine information. This typically requires additional controllers or devices to decipher the information.
Mid-Level Interface:
This pertains to machines where some information is already available through indicators and specific electrical outputs. I/O modules or stack light detector modules are needed to translate this information into a readable format for the host.
High-Level Interface:
This is the most straightforward interface, where all machine information is already available and stored in the controllers or PLCs. If the I/O addresses are known, data such as downtime, machine status, duration of downtime, cycle time, and error codes can be easily retrieved.
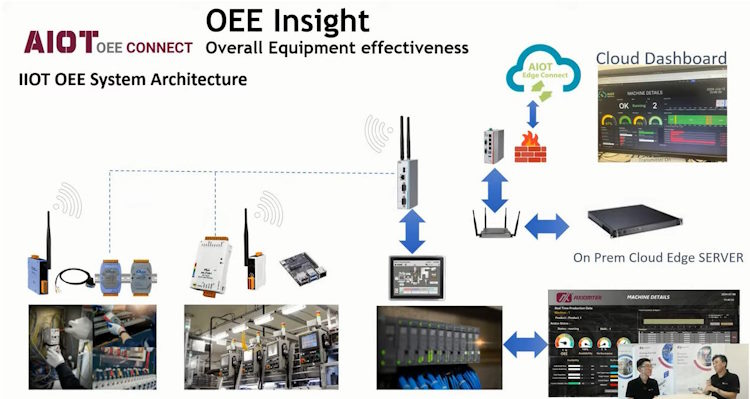
AIOT OEE Insight Connect
AIOT OEE Insight Connect is an OEE tracking system designed to provide users with an online, real-time OEE index and unique insights into their machines or processes. This facilitates continuous process improvement to achieve optimal efficiency. Key benefits of this system include:
Detailed Tracking: The system can track downtime and quality issues in detail, providing data that can be used for future improvements.
Bottleneck Identification: It helps identify process bottlenecks and offers solutions to address them, leading to better overall effectiveness.
Additional features:
Andon Assistance Tools: These tools allow users to track responses and maintenance details, which can be used to implement better preventive measures.
Custom AI-Assisted Workflow: The system engages AI analytics to provide forecasts and early warnings, suggesting actions to ensure that targeted KPIs are consistently met.
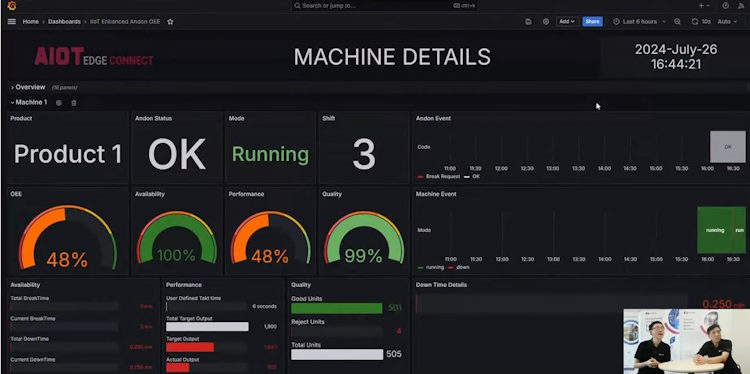
AIOT OEE Insight Connect Local SCADA Dashboard interface let u have a a better real-time visualization of data and Reporting.
Demonstration of the AIOT OEE insight Connect on the Cloud Platform.
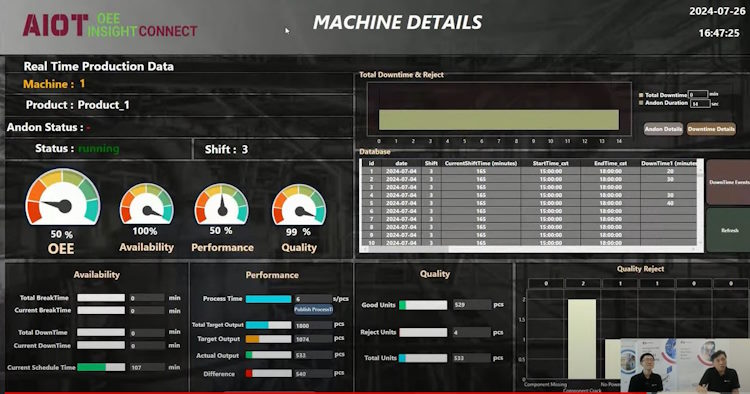
To watch our sharing on the youtube click at the link below:-