

The pressure, an important process parameter that require accurate measurement must not be forgotten in one of the IIoT sensors where it is widely used in the industries.
We highlighted two types of commonly used sensor namely, Strain gauge sensors and Piezoelectric sensors. These sensors are used in many instrument and apparatus.
Piezoelectric Sensor:
Principle: Piezoelectricity is the electric charge that accumulates in certain solid materials (like crystals, certain ceramics, and biological matter like bone) in response to applied mechanical stress. The word “piezoelectricity” means electricity resulting from pressure.
Function: When pressure is applied to a piezoelectric material, it generates a voltage proportional to that pressure. This voltage can then be measured and used to determine the amount of pressure applied.
Applications: Due to their ability to respond to fast changes in pressure, piezoelectric sensors are often used in dynamic applications. They are found in many applications including:
Measuring dynamic pressure changes in gases and liquids.
Detecting the force of impact in automotive airbag systems.
In musical pickups, especially for acoustic instruments.
In some microphones to detect sound waves.
Strain Gauge Pressure Sensors:
Principle: A strain gauge consists of a conductive pattern (often made of a metallic foil) that is affixed to a flexible backing. When this pattern is stretched or compressed, its electrical resistance changes.
Function: When pressure is exerted on a diaphragm or membrane, it deforms (or strains). A strain gauge attached to this diaphragm will also deform, leading to a change in its resistance. This change in resistance is proportional to the pressure exerted on the diaphragm. By measuring this change in resistance, the applied pressure can be determined.
Applications: Strain gauge pressure sensors are widely used due to their reliability and stability. They are found in various applications including:
Industrial process monitoring and control.
Aerospace and automotive sensors.
Medical devices for monitoring blood or fluid pressures.
Load cells for weight measurement.
Both types of sensors come with their own sets of advantages and limitations. While piezoelectric sensors excel at measuring dynamic pressures over short durations, strain gauge sensors are often preferred for stable, continuous pressure measurements.
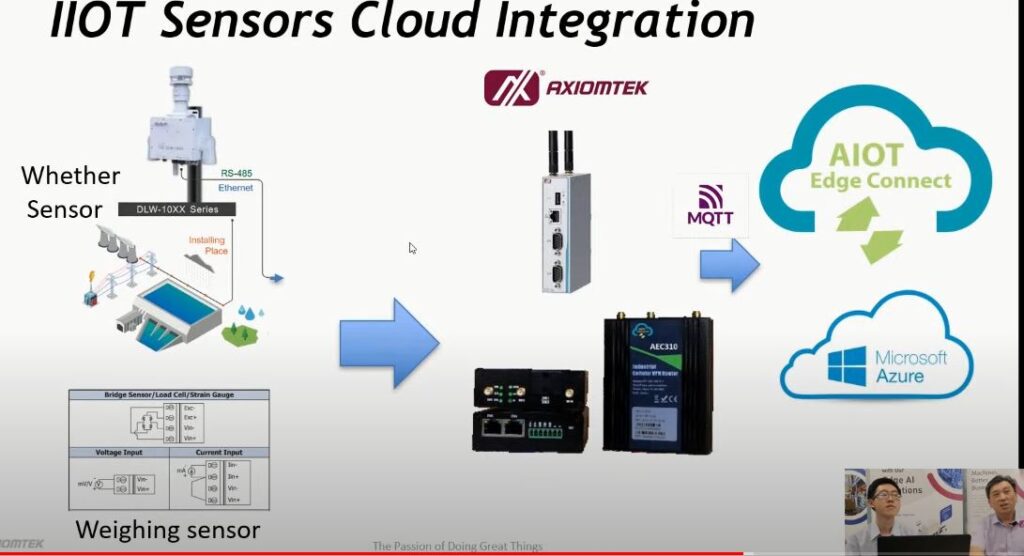
Watch in detail sharing on the Aiotmission youtube channel with the link below: