Understanding the Six Big Losses in Manufacturing: A Roadmap to Greater Efficiency
When you step onto a production floor, you’re immediately immersed in an atmosphere of intensity and focus. It’s a space where every individual, machine, and process is aligned with a singular purpose: maximizing output. Love it or not, this relentless pursuit of efficiency forms the core of manufacturing operations.
In this high-pressure environment, companies rely on metrics to track and enhance productivity. Among these, one metric stands out as the gold standard: Overall Equipment Effectiveness (OEE). OEE is a universal benchmark in manufacturing, measuring how well a production process performs using the formula:
OEE = Availability × Performance × Quality.
This formula distills productivity into three essential components, providing a comprehensive view of where improvements can be made. The concept of OEE was introduced by Seiichi Nakajima, a visionary in manufacturing and the creator of the Total Productive Maintenance (TPM) system in the 1960s. His work laid the foundation for Japan’s global reputation for producing high-quality and efficient products.
But OEE is not just about measuring outcomes. It’s a tool for driving continuous improvement, highlighting inefficiencies that need to be eliminated. While the goal is to maximize Availability, Performance, and Quality, there’s another critical angle: focusing on minimizing losses that impede productivity. This perspective led to the identification of the Six Big Losses, introduced under the TPM framework in the 1970s.
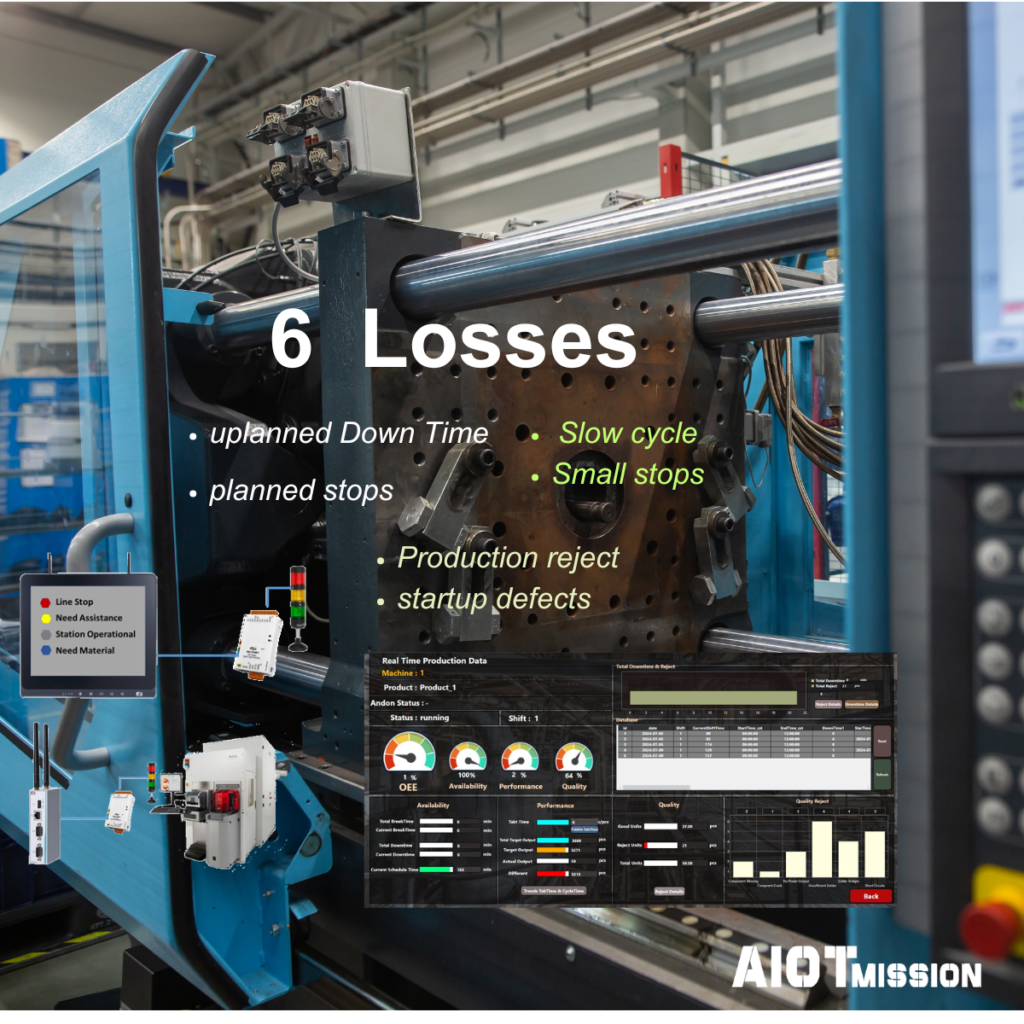
What Are the Six Big Losses in Manufacturing?
The Six Big Losses highlight the most common inefficiencies that prevent manufacturing processes from operating at their full potential. Each loss directly impacts OEE by reducing Availability, Performance, or Quality. Let’s break them down:
- Unplanned Stops
- These occur due to unexpected equipment failures or breakdowns.
- The result is significant downtime, reducing overall Availability.
- Planned Stops
- These include setup changes, routine adjustments, and equipment calibration.
- While planned, they still cut into valuable production time.
- Small Stops
- Minor disruptions such as waiting for materials, operator delays, or sensor misalignments.
- Often ignored, these small interruptions accumulate and affect Performance.
- Slow Cycles
- When machines or processes run below their optimal speed.
- Causes include wear and tear, improper settings, or operator inefficiencies.
- Production Rejects (Defects)
- Defective products generated during normal production runs.
- These affect both Quality and resource efficiency.
- Startup Rejects (Startup Losses)
- Waste created during the startup phase, when machines are stabilizing or processes are fine-tuned.
- Common in operations requiring warm-up or adjustments.
Why the Six Big Losses Matter
Addressing the Six Big Losses is essential for improving OEE. Each loss represents wasted time, resources, and effort—factors that can be minimized with targeted strategies. By tackling these inefficiencies, manufacturers can significantly increase Availability, optimize Performance, and ensure consistent Quality, driving their processes closer to peak potential.
Conclusion
The Six Big Losses provide a practical framework for diagnosing and resolving inefficiencies in manufacturing. By leveraging technologies like IoT and AI, manufacturers can systematically reduce these losses, boost OEE, and achieve unparalleled productivity and quality.
In future discussions, I’ll take a closer look at each of these losses, diving into real-world examples and exploring how cutting-edge solutions are making manufacturing smarter and more resilient. Stay tuned! have a nice weekend.
CC Lee ( Founding CEO) , Tan Kien Leong ( Co-founding CEO) Live session Tech Talk discussion about how AI can maximize efficiency in Smart Manufacturing