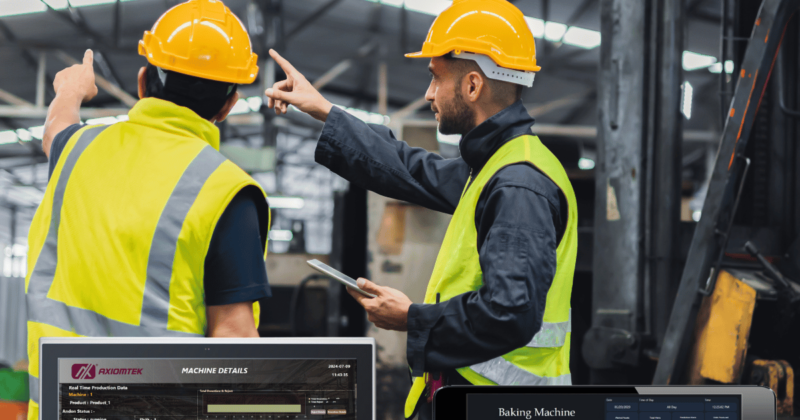
The 6 Big Losses in OEE – Deep Dive into Unplanned Downtime
The 6 Big Losses in OEE – Deep Dive into Unplanned DowntimeIn the world of manufacturing, where efficiency defines competitiveness, OEE (Overall Equipment Effectiveness) serves as a critical performance benchmark. Among the six major losses that OEE identifies, Unplanned Downtime stands out as a particularly disruptive and costly factor — especially in modern, automated environments.Let’s take a closer look at what unplanned downtime really means, its cascading effects on operations, and how manufacturers can tackle it more effectively using predictive AI-powered maintenance.What Is Unplanned Downtime?Unplanned downtime refers to any unexpected stoppage of production caused by equipment failure or unforeseen malfunctions. Unlike scheduled maintenance or planned shutdowns, these interruptions catch production teams off guard — causing a sudden halt in operations and often requiring emergency repairs or adjustments.With today's increasing reliance on automation, the risks associated with unplanned downtime have multiplied. For manufacturers operating under lean principles or Just-in-Time (JIT) strategies, even a short delay can have a "cabin effect" — where a minor...