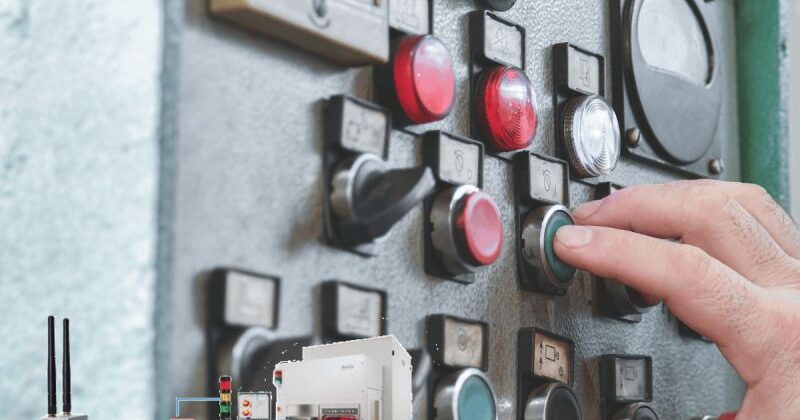
Six key losses in OEE -The Planned Stop
The Planned Stop - Six OEE Big Losses
We can understand unplanned downtime, but why planned stop? 🤔In manufacturing, planned stops represent a major category of production losses and it is part of the OEE six big losses. These are intentional halts in machine operation—such as for model changes, tool changes, or scheduled maintenance—that can heavily impact OEE (Overall Equipment Effectiveness) if not managed properly.A key tool in managing and visualizing these stops is the Andon system—a real-time visual indicator (typically using stack lights with 3 or 4 colors) that communicates machine or process status directly from the production floor. A red or blue light, for instance, may signal a planned stop, alerting operators and maintenance teams in real time.While planned downtime is necessary, poor planning or execution can erode process availability and drag down your OEE score. That’s why tracking and optimizing these stops is vital.Common Causes of Planned Stops:* Model or Tool Changes – Switching between product variants requires precise...