IOT Sensor Technologies for Smart Manufacturing
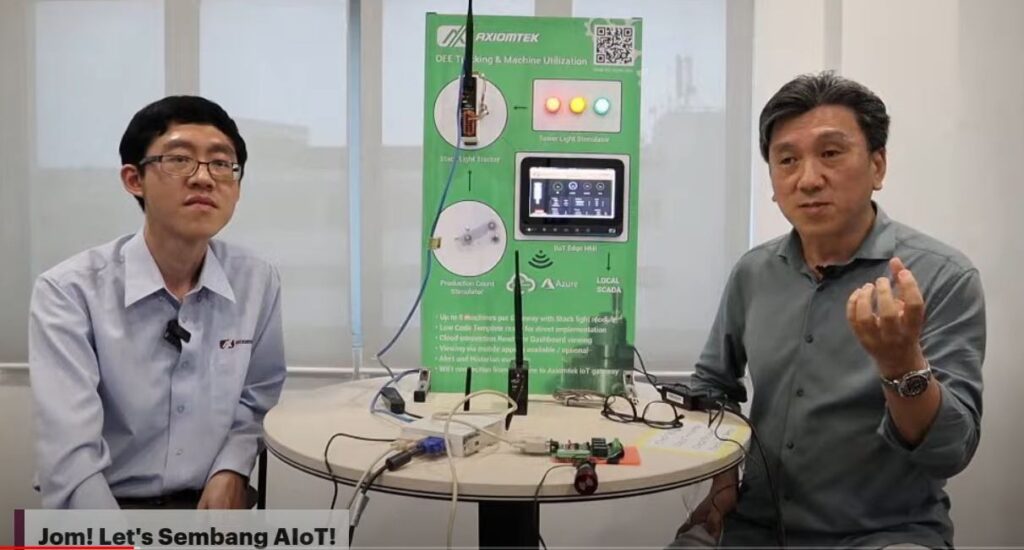
During the recent “Sembang AIOT” episode 38, Once again at AIoTmission, we did a deep dive into the fundamentals of IOT technologies that relate to Smart Manufacturing. There are several topics that we covered this round as below:-
1. Fundamental of IOT relate to the Industries 4.0’s design principal.
2. The roles of IOT in industry 4.0
3. IOT sensors technologies and communication protocols
4. Example of IoT applications in Smart Manufacturing.
1. Fundamentals of IoT in the Manufacturing Environment: Unveiling Industry 4.0’s Design Principles
In this section, we delve into the foundational aspects of Industrial IoT (IIoT) and how it aligns with the core principles of Industry 4.0. Explore the seamless integration of sensors, connectivity, and data analytics that underpin the transformative design principles of Industry 4.0. Understand how IIoT serves as the linchpin for achieving greater efficiency, automation, and intelligent decision-making in the manufacturing landscape.
2. The Pivotal Roles of IoT in Industry 4.0: Orchestrating the Future of Manufacturing
This section elucidates the multifaceted roles that IIoT plays in the context of Industry 4.0. Delve into its pivotal contributions to the convergence of digital and physical systems, the creation of interconnected ecosystems, and the facilitation of real-time data-driven decision-making. Explore how IIoT serves as a catalyst for the evolution of smart factories, predictive maintenance, and overall operational excellence within the industrial realm.
3. IoT Sensors Technologies and Communication Protocols: Building the Nervous System of Smart Manufacturing
Unravel the intricate web of sensor technologies and communication protocols that form the nervous system of smart manufacturing. From RFID and NFC to MQTT and CoAP, explore the diverse array of communication protocols powering seamless data exchange between devices. Dive into the world of sensors, examining their types, functionalities, and how they collectively empower Industry 4.0 by providing real-time insights, enabling condition monitoring, and fostering a more responsive and adaptive manufacturing environment.
4. Examples of IoT Applications in Smart Manufacturing: Realizing the Industry 4.0 Vision
Illustrate the tangible impact of IIoT through specific examples of its applications in smart manufacturing. Explore use cases such as predictive maintenance, asset tracking, supply chain optimization, and quality control. Highlight how IIoT transforms traditional manufacturing processes into dynamic, data-driven ecosystems, fostering agility, innovation, and a competitive edge in the evolving industrial landscape.
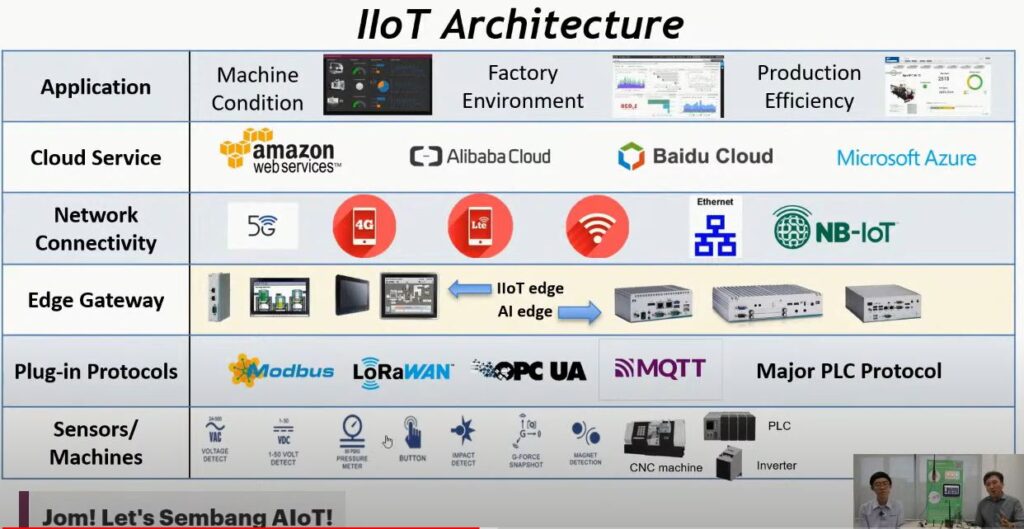
We discussed the architecture of industrial IoT in a deeper level as follows:-
Industrial IoT (IIoT) architecture typically consists of multiple layers or levels, each serving a specific purpose in facilitating the seamless integration of devices, data, and applications within an industrial environment. The architecture is often organized into several layers, and these layers can vary slightly depending on the specific framework or model being followed. Here’s a general overview:
Device Layer (Sensing Layer):
This is the bottommost layer where physical devices, sensors, and actuators are located.
Devices collect data from the industrial environment, such as temperature, pressure, vibration, and other relevant parameters.
Sensors and actuators are responsible for interfacing with the physical world and converting real-world events into digital data.
Communication Layer:
The communication layer facilitates the transfer of data between devices and the higher layers of the IIoT architecture.
It involves communication protocols, such as MQTT (Message Queuing Telemetry Transport) or CoAP (Constrained Application Protocol), ensuring efficient and secure data exchange.
Gateways may be present to aggregate and preprocess data before transmitting it to the upper layers.
Edge Computing Layer:
The edge computing layer is responsible for processing and analyzing data closer to the source (at the edge of the network) before sending it to the cloud or a central server.
Edge computing reduces latency, saves bandwidth, and enables faster decision-making for critical applications.
Edge devices may host lightweight analytics, machine learning models, or data filtering mechanisms.
Platform Layer:
The platform layer is where data is stored, managed, and processed in a centralized manner.
It involves cloud platforms or on-premises servers that provide storage, computing power, and services for handling massive amounts of data generated by industrial devices.
Analytics tools, databases, and middleware components are often part of this layer to extract insights from the data.
Application Layer:
The application layer represents the software applications, services, and user interfaces that leverage the processed data to deliver specific functionalities.
Applications may include monitoring and visualization tools, predictive maintenance applications, and other software solutions tailored to the industrial use case.
Human-machine interfaces (HMIs) and control systems may also be part of this layer.
The layered architecture of IIoT provides a structured approach to designing and implementing industrial systems, ensuring scalability, interoperability, and efficiency. This framework allows for flexibility in choosing technologies for each layer and enables the seamless integration of new devices and applications into the industrial ecosystem.
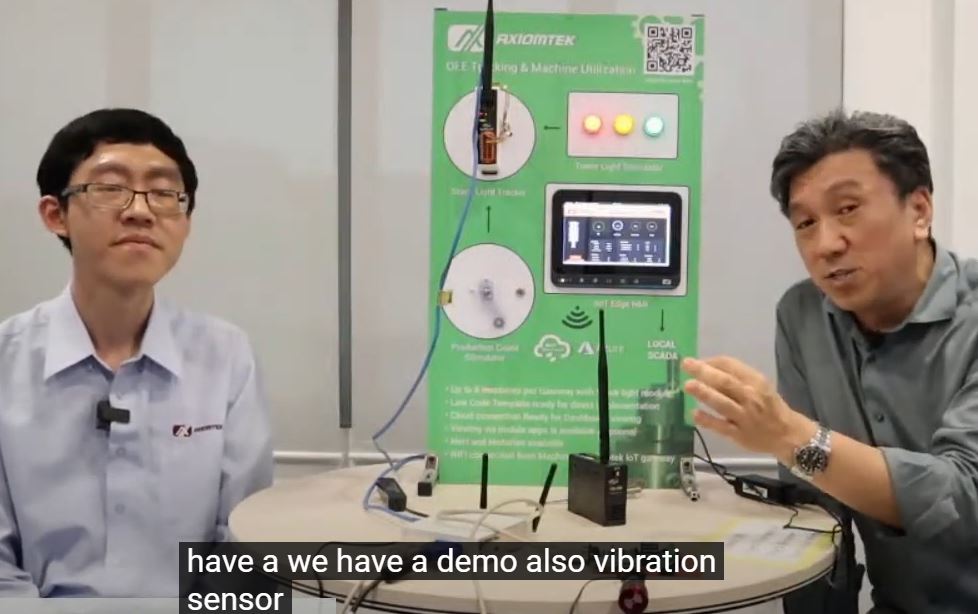
In the live session, we demonstrated IoT programming tool, the Node Red that built from node JS and simulated OEE system with some key components like Stack light modules and other IoT sensors modules.
Implementing an Internet of Things (IoT) system can significantly enhance the development and functionality of Overall Equipment Effectiveness (OEE) tracking systems in the manufacturing environment. OEE is a key performance indicator that measures the effectiveness of manufacturing processes. Here’s how IoT contributes to building a robust OEE tracking system:
Real-Time Data Collection:
Sensor Integration: IoT devices, such as sensors and actuators, can be strategically placed on machinery and production lines. These sensors collect real-time data on factors like machine downtime, production speed, and product quality.
Connectivity: IoT-enabled devices seamlessly transmit data to a centralized system, ensuring that the OEE tracking system is constantly updated with accurate and timely information.
Data Analytics and Monitoring:
Data Processing: The collected data is processed and analyzed in real time. IoT devices enable the handling of large volumes of data, allowing for a comprehensive analysis of machine performance and overall production efficiency.
Machine Learning Algorithms: Implementing machine learning algorithms can help predict and identify patterns related to equipment failures or performance issues, aiding in proactive maintenance and optimization.
Remote Monitoring and Control:
IoT Platforms: Utilizing IoT platforms, manufacturers can remotely monitor equipment performance from anywhere. This capability facilitates quick responses to issues, reducing downtime and improving OEE.
Control Mechanisms: In addition to monitoring, IoT-enabled systems can offer remote control features, allowing operators to adjust parameters or shut down machines in response to potential problems identified through the OEE tracking system.
Predictive Maintenance:
Condition Monitoring: IoT sensors continuously monitor the condition of machinery, detecting variations or anomalies in performance.
Predictive Analytics: By analyzing historical and real-time data, predictive analytics models can predict when equipment is likely to fail. This proactive approach minimizes unexpected breakdowns, leading to increased machine uptime and improved OEE.
Integration with Existing Systems:
ERP and MES Integration: IoT-enabled OEE tracking systems can seamlessly integrate with existing Enterprise Resource Planning (ERP) and Manufacturing Execution Systems (MES). This integration ensures a cohesive flow of information across the entire production ecosystem.
Performance Visualization:
Dashboard and Reporting: IoT-powered OEE systems provide intuitive dashboards and reports that visualize key performance metrics. This allows stakeholders to quickly assess the efficiency of manufacturing processes and identify areas for improvement.
By leveraging IoT technologies in OEE tracking systems, manufacturers can achieve a more agile, responsive, and efficient production environment, leading to improved overall equipment effectiveness and, consequently, enhanced productivity.
Watch the session at our Youtube channel:-